回首过去二三十年,中国家电行业经历了从无到有、从跟随到领跑的转变。作为中国家电行业的一份子,GMCC美芝也与合作伙伴用坚守与创新不断书写出中国家电发展的历史。从1996年首台空调压缩机下线,到2002年产量突破1000万台,从2010年产销突破一亿台,再到2024年第10亿台下线,美芝不断突破行业“天花板”,同时也实现从单一产品到消费电器零部件的全面布局,成为消费电器核心零部件系统级解决方案供应商。

GMCC美芝空调压缩机能够取得行业“第一品牌”及“隐形冠军”等成绩,除众多空调客户的支持外,也离不开积极拥抱多元化市场需求的勇气,以及每年交付超一亿台空调压缩机的“底气”。而高品质制造与大规模交付、供应背后,则离不开美芝在数字化转型上的持续深耕与实践。
GMCC美芝围绕品质卓越、敏捷交付、绿色安全三大主轴,全面夯实制造基础,构建可持续、零断点全场景数智驱动能力,并朝着打造世界级智能工厂而努力。在生产过程中,美芝将多种ICT技术应用到原有的生产要素中,从而引起业务的创新、重构,并在转型过程中不断积累和形成数字资产和数字实践,构建数据优势、经验,让竞争力持续领先。
GMCC美芝科技产业园:全流程数字化,重塑生产与运营的新格局
位于广东佛山顺德区的GMCC美芝科技产业园(美芝杏坛工厂)于2023年正式投产,是GMCC美芝全球范围内面积最大、智能制造水平最为领先的工厂之一。在建设之初,美芝杏坛工厂即以打造消费电器领域的“μ级精密智能制造”标杆工厂为目标,从智能排产、智能品质、智能物流、数字工艺、设备管理、绿色能源、智慧园区、智慧实验室和数据运营九个维度进行打造,各种数字化技术与应用则帮助其成功达成这一目标。
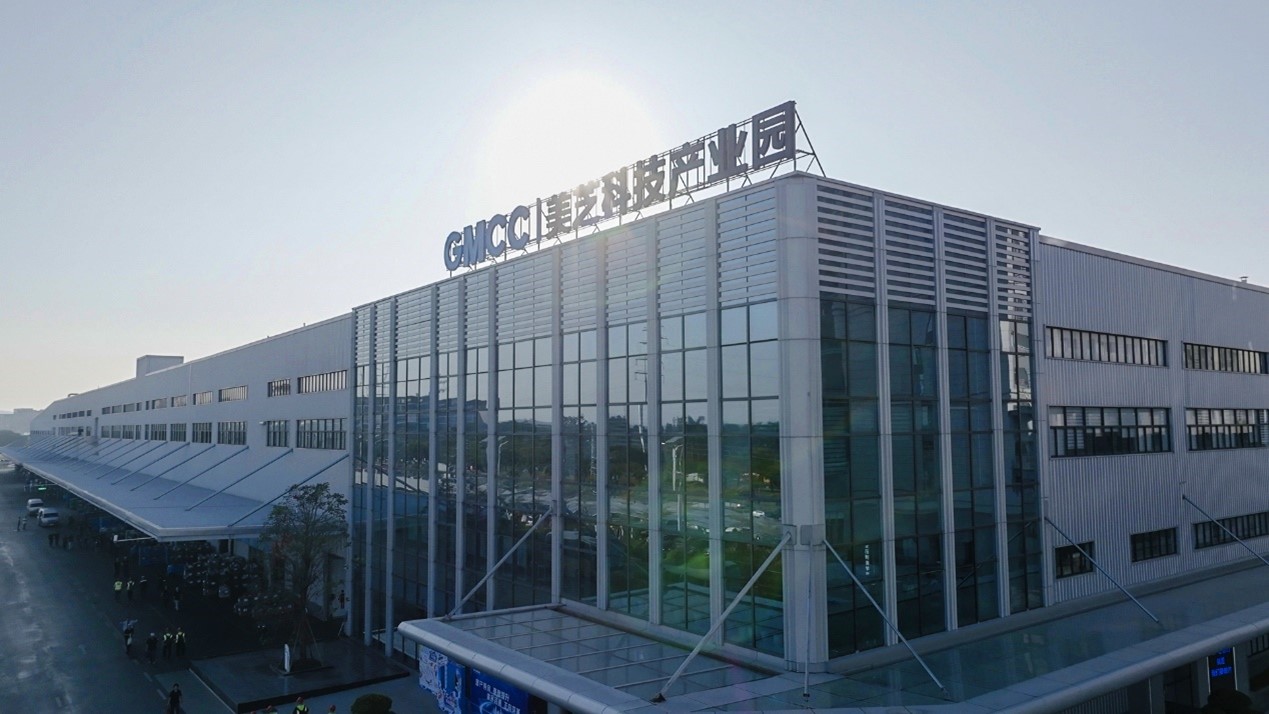
以数字化为底,从销售订单开始,数字化就已经开始在美芝杏坛工厂发挥作用且无处不在。订单自动同步到计划系统,排产系统则像一位精准的指挥官,根据客户需求分解物料需求和生产计划。采购订单随即下达指令给供应商,实现生产和配送物料无缝衔接。工厂各生产系统则接收到详细的生产工单,生产任务随即开始执行。
与此同时,在数字化平台MLS系统的指挥下,生产中用到的各种物料,也开始由AGV、RGV、无人叉车等智能物流装备配送,实现物流的智能调度和实时监控。这一智能排产与物流体系,如同工厂的神经网络,确保了生产流程的顺畅与高效,实现了从订单接收到产品交付的全链条智能化管理。
在工艺与品质的提升上,得益于不断更新的数字化技术,美芝利用仿真工具能够提前验证生产等问题,确保改善措施有效,核心工艺参数通过数字化系统监控,确保加工状态最优;AI视觉与自动检测技术的结合,如同工厂的“智慧之眼”,守护产品细节,确保品质卓越。条码技术为每件产品赋予“身份证”,实现全流程透明化管理。
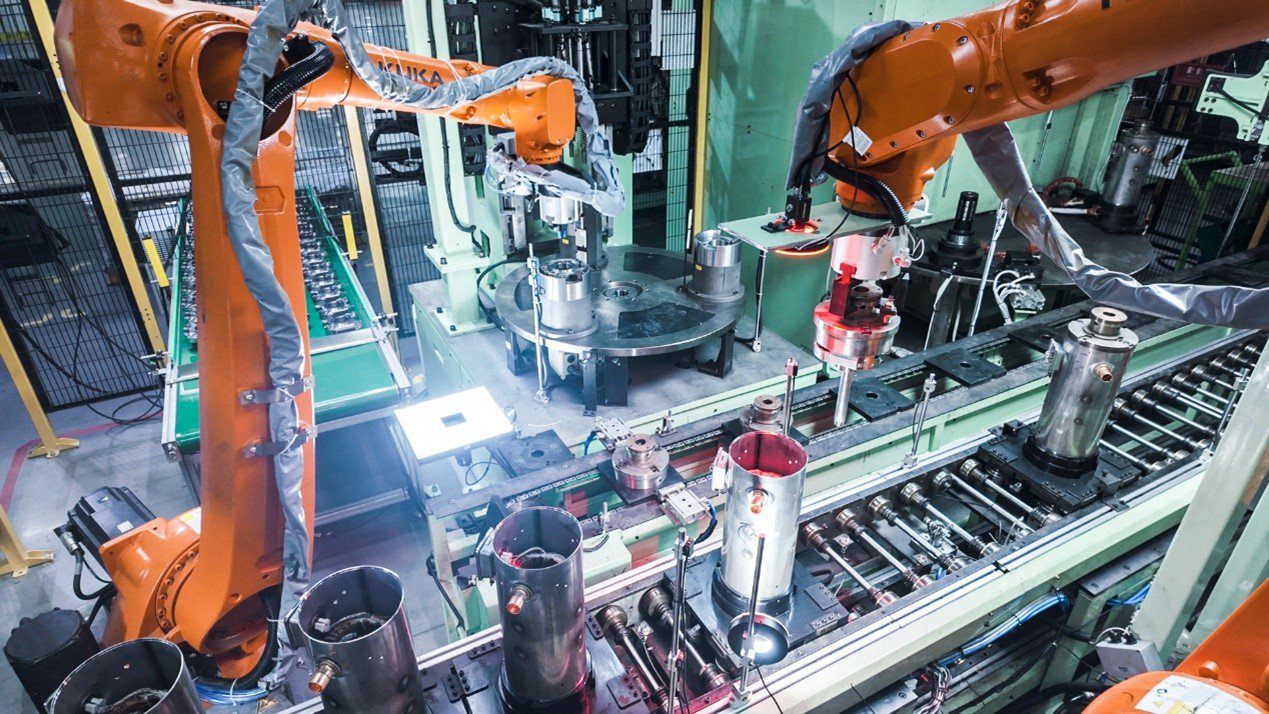
同样,作为工厂智慧转型升级的重要引擎,美芝杏坛工厂也将数字化融入了智慧运营的各个环节,覆盖现场管理、机加工设备和厂区用能、实验室等场景,构建起绿色的智慧运营体系。
如通过传感器与系统数字模型实时监测核心加工设备的健康度,以AR远程维护技术降低设备故障率,提升维护效率,确保整条产线上的“工业母机”高效、稳步运行;在现场管理方面,美芝以DMS系统搭建高效数字桥梁,并依托五级会议机制捕获并深入分析现场问题,确保问题及时解决。
在数字化绿色用能上,美芝采用智能仪表实时采集能耗数据,通过算法模型实现用能优化,降低能耗成本。在智慧实验室中,美芝通过数字化实现实验数据可实时监控、精准分析,实验结果达成自动分析,为产品品质提供坚实保障。
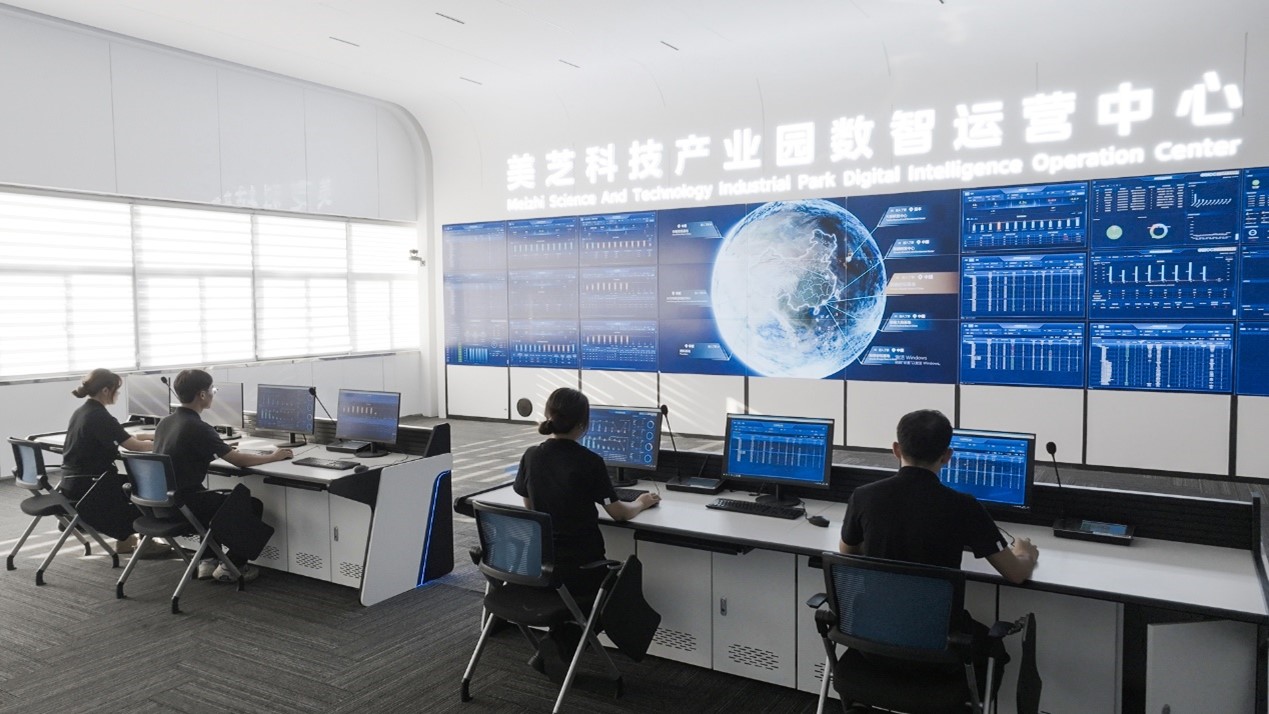
数字化与业务的深度融合,使美芝杏坛工厂取得了显著成就:单线6秒下线一台压缩机,远超行业水平,交付周期大幅缩短。
GMCC美芝芜湖工厂:以数字化打造“零不良流出”标杆产线
在消费电器领域,在大规模交付背景,如何提升产品品质,大幅度改善交付质量相当困难。尤其是海量交付情况下,如何保持产品的一致性,是全行业的难点、痛点。
作为空调压缩机领域绝对的领跑者,美芝历经多年数字化实践,并在芜湖工厂给出了答案:借助于机器学习与大数据分析等智能化技术,联合集团智研院共同打造“智能采集、智能分析、智能预警、智能管控、智能预测、智能决策”六智“零不良流出”品质标杆线,包括行业首创的上轴承刻印二维码、铆接异常AI检测、三点焊AI检测、定转子间隙AI检测、设备预测性维护,以及通过AI智能算法对测试参数阈值进行自适应调整,并结合SCADA、MES系统,实现测试参数的云端储存及下发,以及利用图像积差原理,对测试结果判定的智慧性能线。针对行业难题,美芝经过实践不仅形成品质管理与精益生产相结合的“方法论”,更创造了百万台交付“零不良流出”的行业实绩。
从源头把控产品质量,智能管理造就品牌新模式,美芝空压芜湖工厂致力于成为工业4.0智造时代的领先者。围绕μ级加工能力与数智化智能品控标杆线,美芝空压芜湖工厂通过μ级设备引进、μ级工艺技术、μ级检出能力,实现产品μ级加工水平和装配效果。
为不断精进产品品质并强化市场竞争力,美芝倾听客户声音(VOC)并以其驱动生产的改善(VOP)。如针对客户反馈较高的“设备不制冷或效果差、外机噪音大、不启动”等问题,迅速找出根源所在并以数字化手段给出整改措施。包括压缩机一码溯源、智能铆接工位、泵体扭矩检测、智能充磁检测、三点焊检测、定转子间隙检测、壳体焊接在线监测等。正式借助这些数字化手段,美芝芜湖工厂对压缩机生产线实施了全面的数字化革新,标志着工厂成功跨越了从人工操作到智能控制、从模糊管理到精准管理的鸿沟。
以压缩机一码溯源为例,在美芝芜湖工厂,每一台压缩机都被赋予了独特的标识——一枚包含生产信息的二维码。二维码如同压缩机的身份证,记录了它的生产流程、质量检测数据等关键信息。包括关键岗位缺少防呆手段以及低级错误导致品质问题,铆接/焊接等工位人工目检导致的缺少一致性和准确性等问题,以及不良品的原因排查缺少生产数据依据等问题,都可以通过二维码查询到相关视觉/振动等性能检测数据、每一台压缩机的生产信息以及全流程数据关联分析等。
通过压缩机一码溯源,美芝芜湖工厂实现了减少和杜绝低级错误的发生,提高产线品质一致性,最终实现总装产线“零不良流出”。
设备SCADA联机率100%,实现智能取数与生产实时透明化,首创设备无纸化智能点检实现设备真正的远程管控,一体化智能检测设备在检出效率快速提升的同时也大大提升检出有效性。借助数字化生产线重塑,美芝芜湖工厂六智标杆线也水到渠成,助力工厂实现了生产全过程的透明化、可视化和可追溯。
工人不仅能实时掌控生产线的运行状态和生产进度,确保产品质量与安全性,同时也有助于质量问题的快速定位和解决,最终助力美芝芜湖工厂在敏捷交付、效率提升及品质、技术领先上保持行业竞争力。
数字化转型对企业意味着多方面的深远影响和变革,GMCC美芝通过深度融合尖端数字化技术以及打造智能制造体系,不仅精准捕捉并满足市场的多元化需求,更在节能减排、管理效能提升及创新能力激发等多个维度上实现了质的飞跃,为整个行业数字化转型提供有益范式。
展望未来,GMCC美芝将推进数字化转型深度与广度,以持续的数字化投入与实践推动中国消费电器制造的可持续发展,携手客户为全球消费者呈献更高品质、更高效率、更绿色的产品与服务。
发表评论